Inside LG Energy Solution's Battery Manufacturing Facility: Unveiling the Secrets of Lithium-Ion Batteries
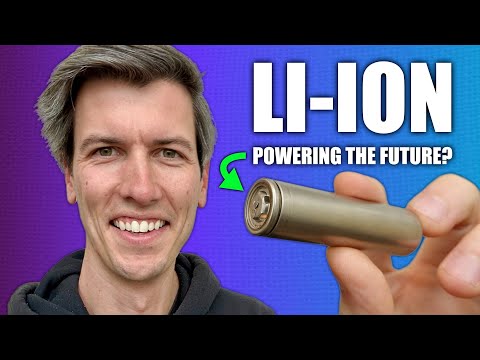
- Authors
- Published on
- Published on
- Name
- By Dushyant
- (@dishs)
In this thrilling video, sponsored by the powerhouse LG Energy Solution, we are granted exclusive access to their battery manufacturing facility in Holland, Michigan. Strap yourselves in, folks, because we're about to embark on a journey to uncover the secrets behind the mighty lithium-ion battery. This technological marvel is revolutionizing the automotive industry, and we're here to answer three burning questions: what is a lithium-ion battery, how does it work, and how is it made?
Picture this: a lithium-ion battery is like a symphony of four key components. We've got the cathode, the anode, the electrolyte, and the separator. These parts work in perfect harmony to deliver the power we need. The cathode and anode, the positive and negative terminals of the battery, exchange lithium ions and electrons. The electrolyte solution facilitates this exchange, while the separator ensures there's no short circuiting going on. Safety first, people!
Now, let's dive deeper into the cathode, the star of the show. When you hear fancy terms like nickel, manganese, cobalt, and aluminum, that's all about the cathode material. It's the most expensive part of the battery, and the most expensive part of an electric car, for that matter. Different chemistries, such as NMC 622, are used in the automotive industry, indicating the composition of the cathode. More nickel means improved energy density, but it can also lead to microcracking and reactivity issues. However, the clever folks at LG Energy Solution have found a way to use higher concentrations of nickel by creating a gradient in the cathode. This results in a particle that's less prone to microcracking and has improved energy density. It's like magic!
But wait, there's more! The anode, typically made of graphite, is where all the lithium action happens. Silicon is making waves in anode chemistries due to its ability to store more lithium, but it comes with its own set of challenges. Silicon tends to expand and contract as the lithium moves in and out, causing headaches for engineers. Next up, we have the electrolyte, a liquid that allows the lithium ions to flow freely within the battery. It must be carefully selected to ensure it doesn't react with other battery materials, has a low freezing point, and a high ignition point. Safety, safety, safety!
Last but not least, we have the separator, the unsung hero of the battery world. This little marvel prevents the positive and negative sides from getting too cozy and causing a short circuit. It has micro pores that allow the lithium ions to flow while cleverly closing up if the battery starts to overheat. Talk about self-preservation!
Now that we have a good grasp on the components, let's unravel the mystery of how it all works. Imagine a battery as a bustling parking lot. During charging, the lithium atom loses an electron to the anode structure and becomes a lithium ion. This ion then travels through the separator, finding a cozy parking spot within the cathode structure, where it happily reunites with an electron. Voila! We have a stable lithium atom. During discharging, this process is reversed, with the lithium ion losing an electron to the surrounding structure and finding its way back to the anode. It's like a dance of ions and electrons, creating the power that propels our electric cars forward.
Now that we've unlocked the secrets of the lithium-ion battery, it's time to venture into the realm of manufacturing. Brace yourselves, because there are a staggering number of steps involved. First, we have electrode manufacturing, where the cathode and anode slurries are mixed and coated onto current collectors. These rolls are then cut into battery-sized pieces. Next up, we have cell assembly, where the battery-sized pieces are laminated, adding the separator and stacking them into layers. The electrolyte is injected, bringing the battery to life. Formation comes next, where the batteries are charged, discharged, and undergo an aging process to stabilize the cells. Finally, we reach the pack process, where individual cells are inserted into modules, wired, and connected. Multiple modules are then added to a pack housing, along with other necessary parts like converters and cooling equipment. The pack is sealed, inspected, and subjected to rigorous tests before being shipped off to car manufacturers.
LG Energy Solution's Michigan facility is a sight to behold, with a capacity of 5 GWh. But that's not all! They're building another facility next door, expected to provide a whopping 25 GWh output. These guys mean business! With over 30 years of experience and an impressive 27,000 battery-related patents, LG Energy Solution is at the forefront of battery technology. They're actively hiring, so if you're looking to be part of this electrifying industry, now's your chance!
In conclusion, this adrenaline-fueled adventure through the world of lithium-ion batteries has shed light on their inner workings and the meticulous process of their creation. Thanks to LG Energy Solution for sponsoring this mind-blowing journey, and thank you all for joining us. If you have any burning questions or epic comments, feel free to leave them below. Stay charged, my friends!
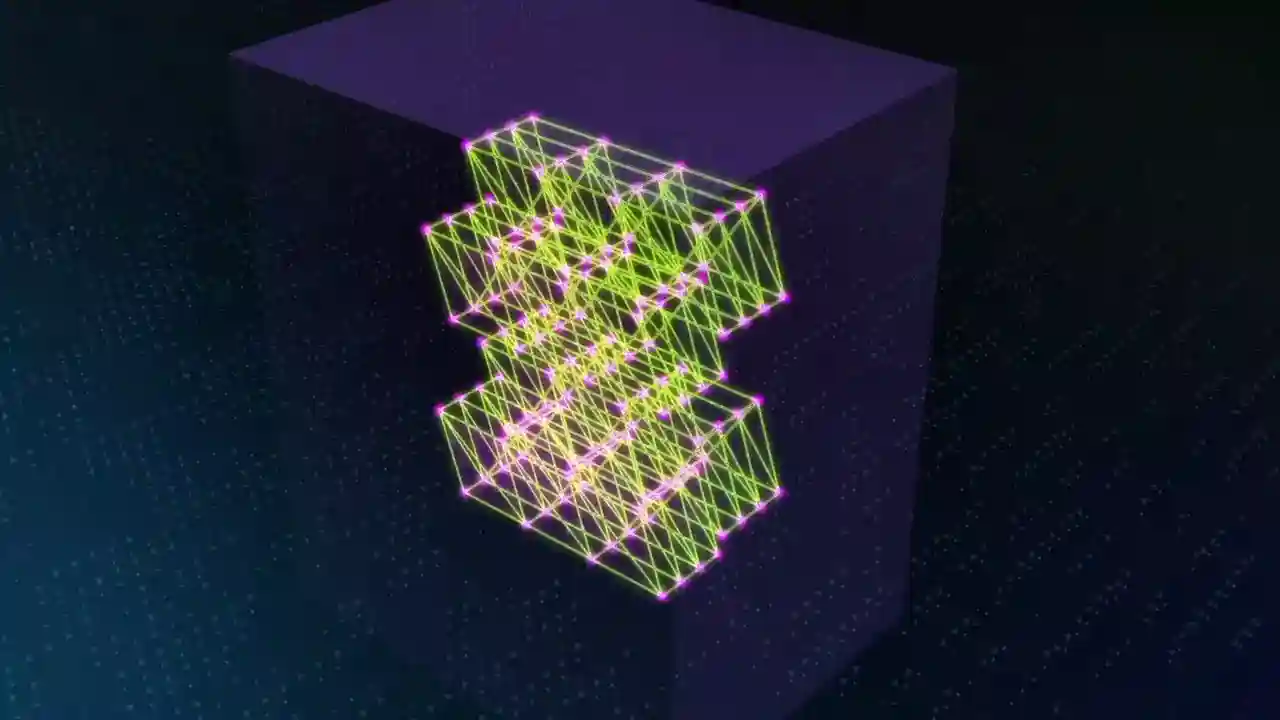
Image copyright Youtube
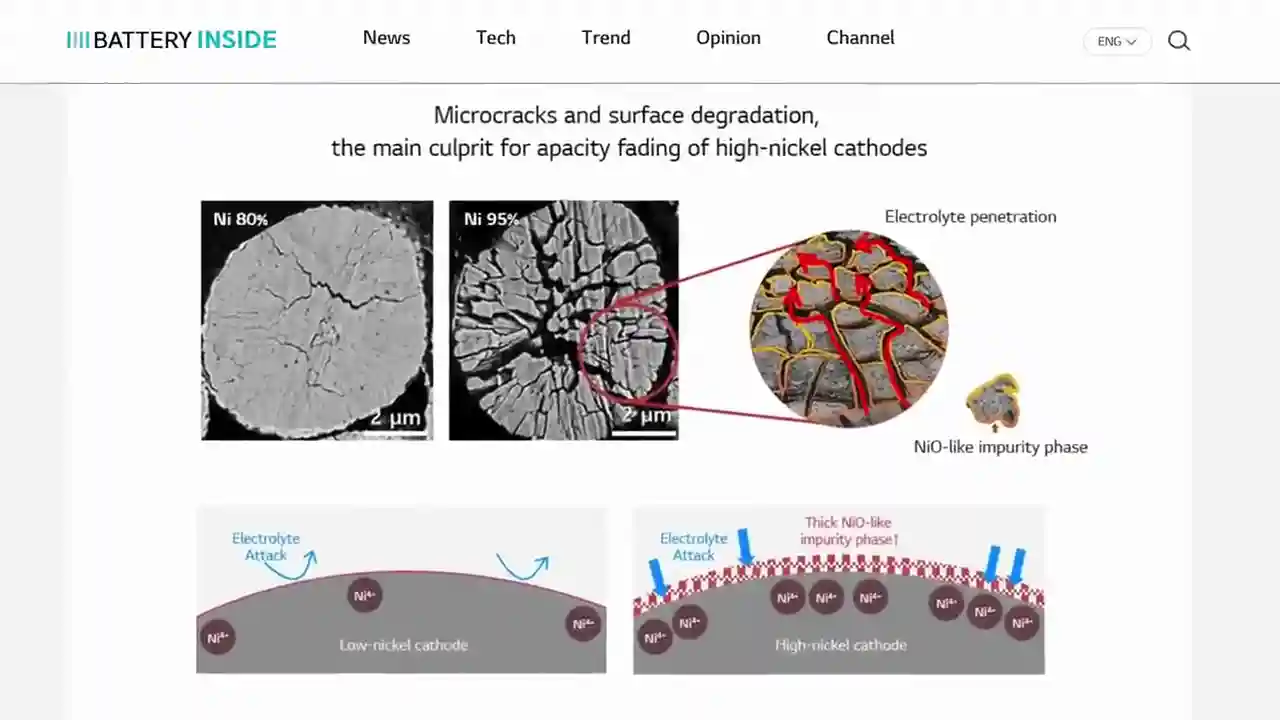
Image copyright Youtube
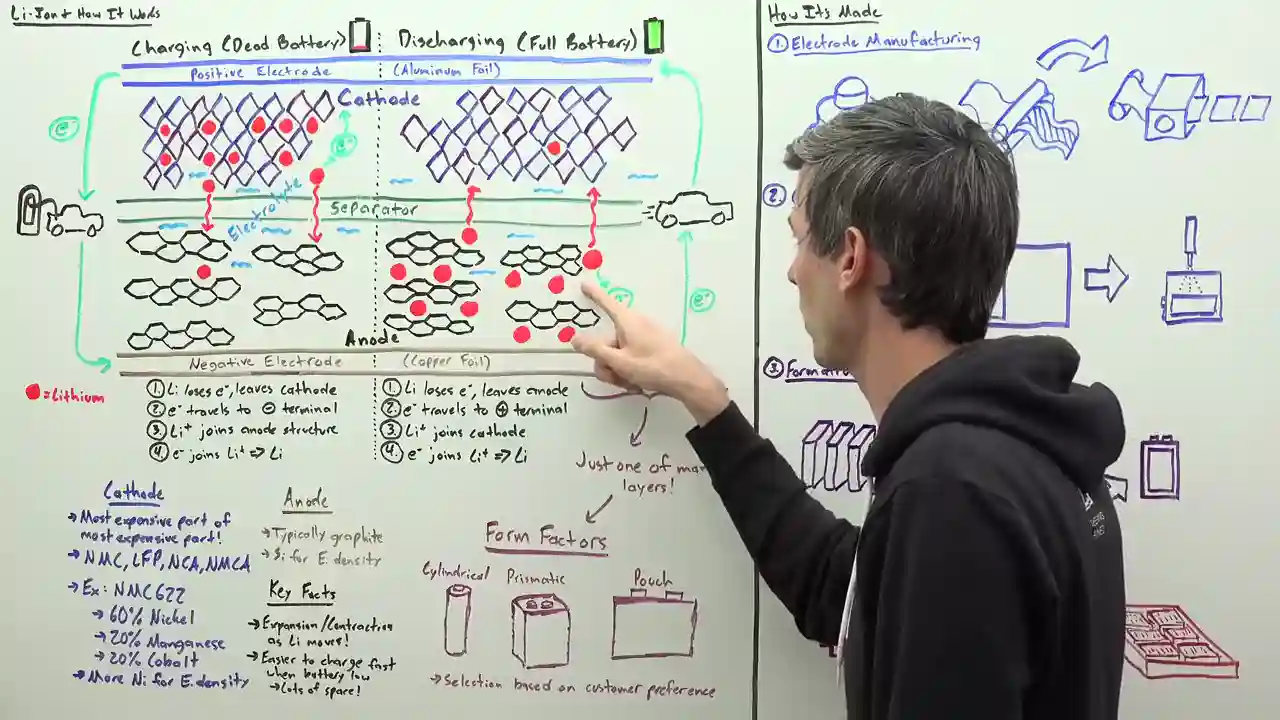
Image copyright Youtube
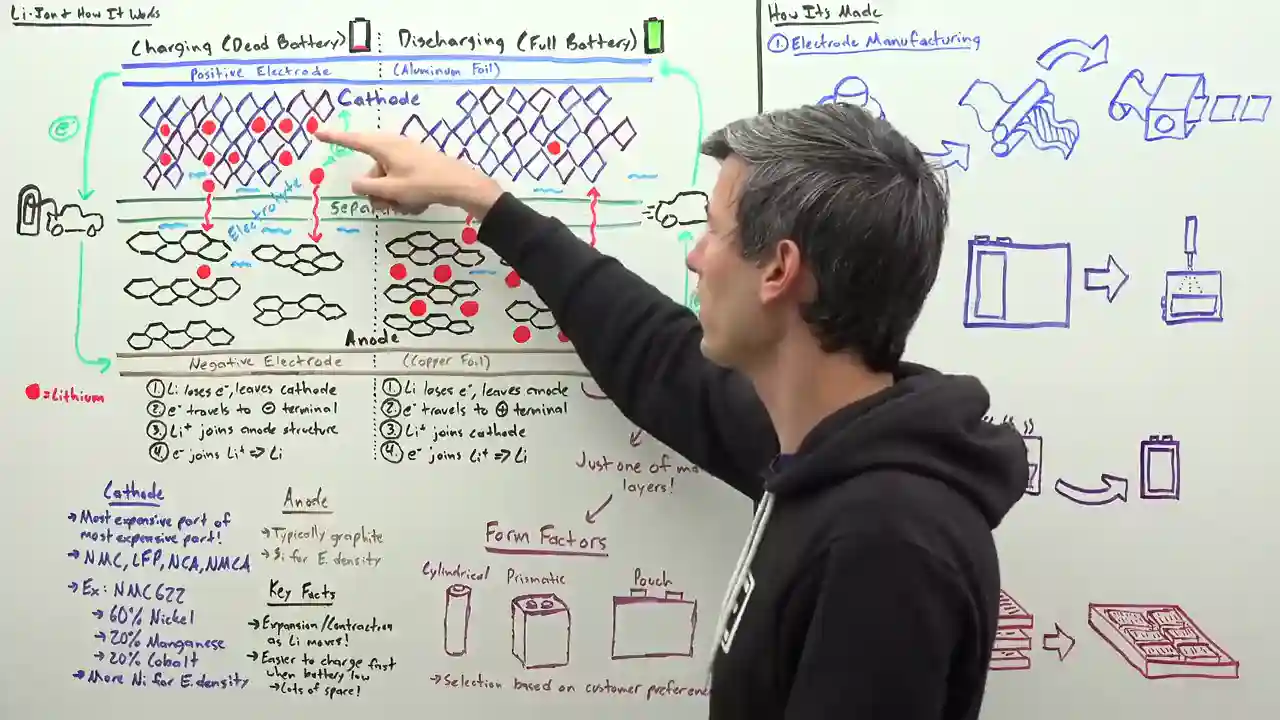
Image copyright Youtube
Watch Everything You Need To Know About Lithium-Ion Batteries on Youtube
Viewer Reactions for Everything You Need To Know About Lithium-Ion Batteries
Viewer praises the channel and its content
Viewer requests more videos on electric vehicle engineering and battery technology
Viewer suggests a video on solid-state batteries
Viewer asks for an analysis of what causes batteries to catch fire
Viewer expresses interest in learning about battery recycling
Viewer provides additional information on battery charging strategies
Viewer suggests a video on battery deterioration
Viewer expresses appreciation for the video and requests more content on materials science
Viewer asks if there is a measurable weight shift in batteries as lithium-ions move through the separator
Viewer requests another video on electric vehicles and their efficiency
Viewer praises the channel as the best content creator
Viewer suggests a video on sodium-ion batteries
Viewer suggests longer videos on the topic
Viewer comments on the presenter's voice
Viewer suggests an interview with Jeff Dahn
Viewer makes a joke comment
Viewer suggests discussing the recycling and decommissioning of batteries
Viewer comments with surprise
Viewer suggests that LFP is a better chemistry than NMC, NCA, and NMCA
Viewer mentions living near the production facility
Viewer asks about the CO2 emissions during battery production
Viewer expresses frustration with Tesla and electric vehicles
Viewer expresses skepticism about current battery technology and suggests alternatives like supercapacitors or high-performance fuel cells.
Related Articles
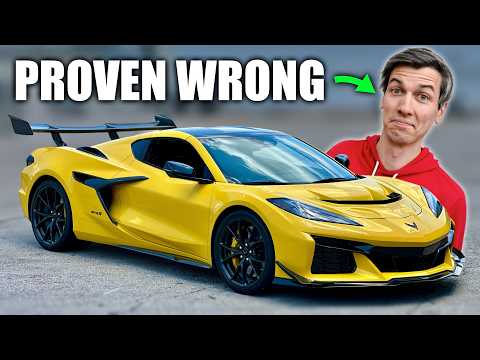
Unveiling Corvette ZR1: Acceleration Secrets and Track Dominance
Engineering Explained reveals the Corvette ZR1's astonishing acceleration, custom launch control secrets, hidden red line, and exceptional handling capabilities, showcasing its dominance on the track.
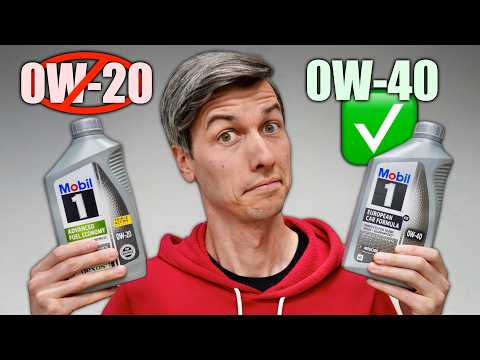
GM Engine Failures: Thicker Oil Solution Revealed
Engineering Explained uncovers GM's engine failures due to manufacturing defects, recommending a switch to thicker oil for optimal engine performance and longevity.
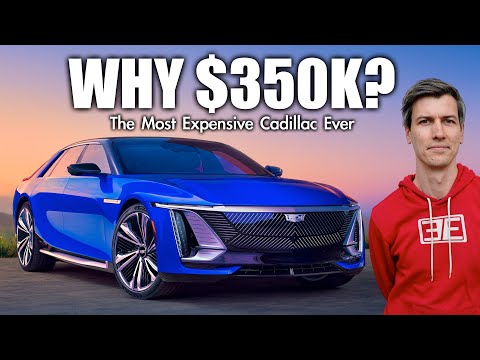
Exclusive Review: Cadillac Celesteic Unveiled - Luxury & Innovation
Experience the Cadillac Celesteic: a $350,000 flagship sedan with 655 hp, 303 mi range, and unique manufacturing techniques like massive aluminum castings and 3D printed metal parts. Discover the luxury of low-volume production and innovative design in this exclusive review.
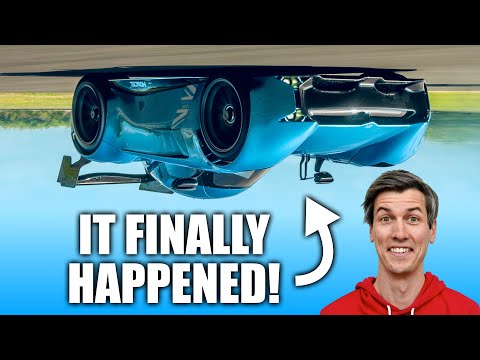
Revolutionizing Downforce: McMerry Spearling's Impact on Racing
The McMerry Spearling revolutionizes downforce creation with fan technology, showcasing remarkable efficiency and potential for Formula E and Formula 1.