Designing a Custom Intake Manifold with AI: Rob Dahm's Journey into Precision Engineering
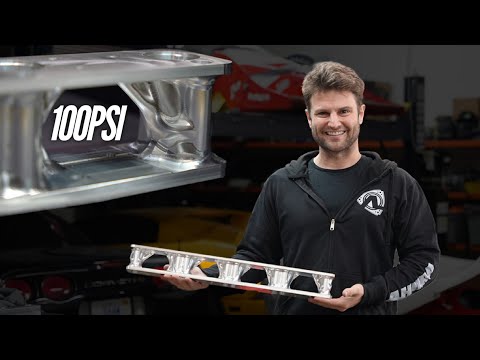
- Authors
- Published on
- Published on
- Name
- By Dushyant
- (@dishs)
In this thrilling episode of Rob Dahm, the team takes on the Herculean task of designing the top of a 12 rotor engine. It's a battle against time, weight, and sheer horsepower as they strive to create something truly mind-boggling. And what's their secret weapon? Artificial intelligence. Yes, you heard that right. They're using AI to craft some of the most insane engine parts you've ever seen.
But let's not get ahead of ourselves. Before they can even think about the AI wizardry, they need to figure out how to get air into the motor. And let me tell you, it's no walk in the park. This is a custom job, my friends. The amount of material, time, effort, and size that goes into this is enough to make your head spin. But the team is determined. They've got their hands on some top-notch aluminum, even if it costs them a pretty penny. And let's not forget about the CNC machine. It may not cut to the edge of the table, but that doesn't stop them. They'll cut a section, shift it over, and cut the other section. It's a dance of precision and ingenuity.
Now, let's talk about the real star of the show: the intake manifold. This piece of art is where the power is made, where the air-fuel ratio comes together in perfect harmony. It's a work of engineering genius. And the team knows that if they were to outsource this job, it would cost them an arm and a leg. So they take matters into their own hands, using the AI to design the perfect manifold. They start with the basics, creating the flanges and the necessary holes. Then, they expand on that, creating walls and cutting out the minimum required material. It's a delicate dance of specifying where the material should be and where it shouldn't. And the result? A diamond in the rough, a piece of billet aluminum that can handle the immense pressure and forces it will face.
But it's not all smooth sailing. The team encounters some setbacks along the way. Ethan's first attempt is a disaster, rendering the piece unsalvageable. But they don't let that deter them. They push forward, learning from their mistakes and making improvements. And in the end, they emerge victorious, with a beautifully machined intake manifold that is both lightweight and strong. It's a testament to their perseverance and their willingness to embrace new technologies. So strap in, my friends, because this is one wild ride you don't want to miss.
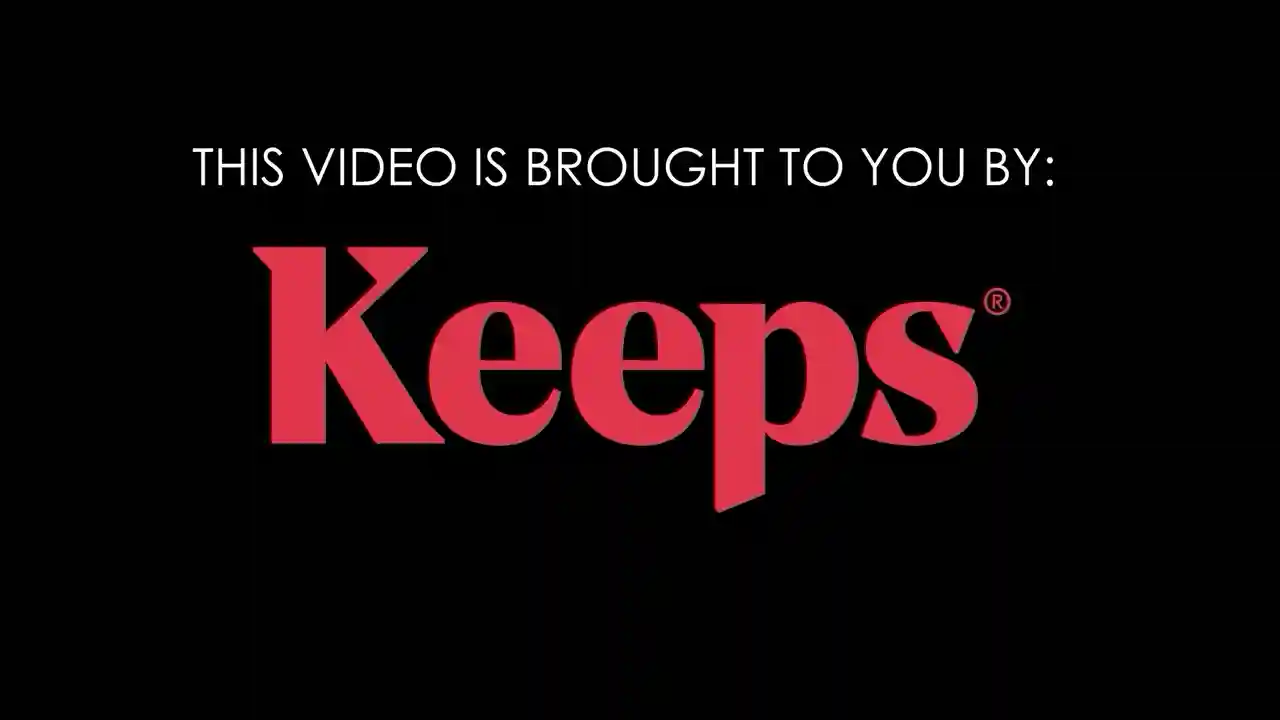
Image copyright Youtube
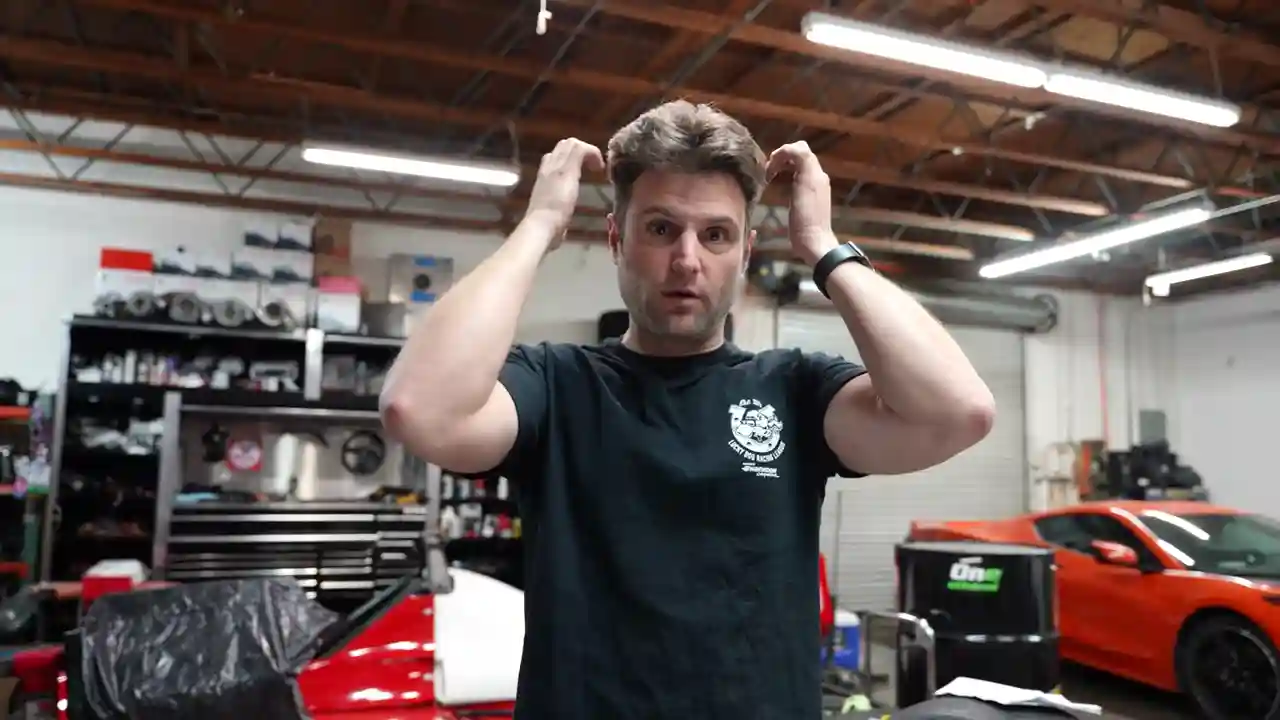
Image copyright Youtube
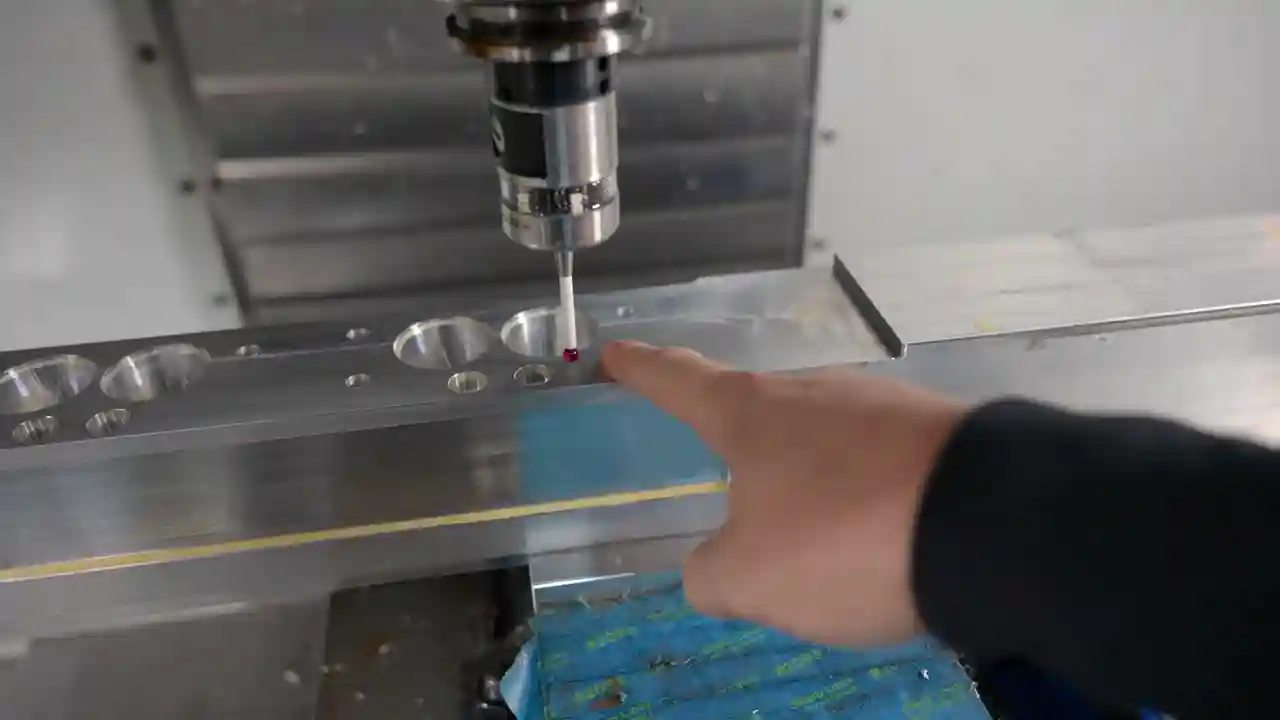
Image copyright Youtube
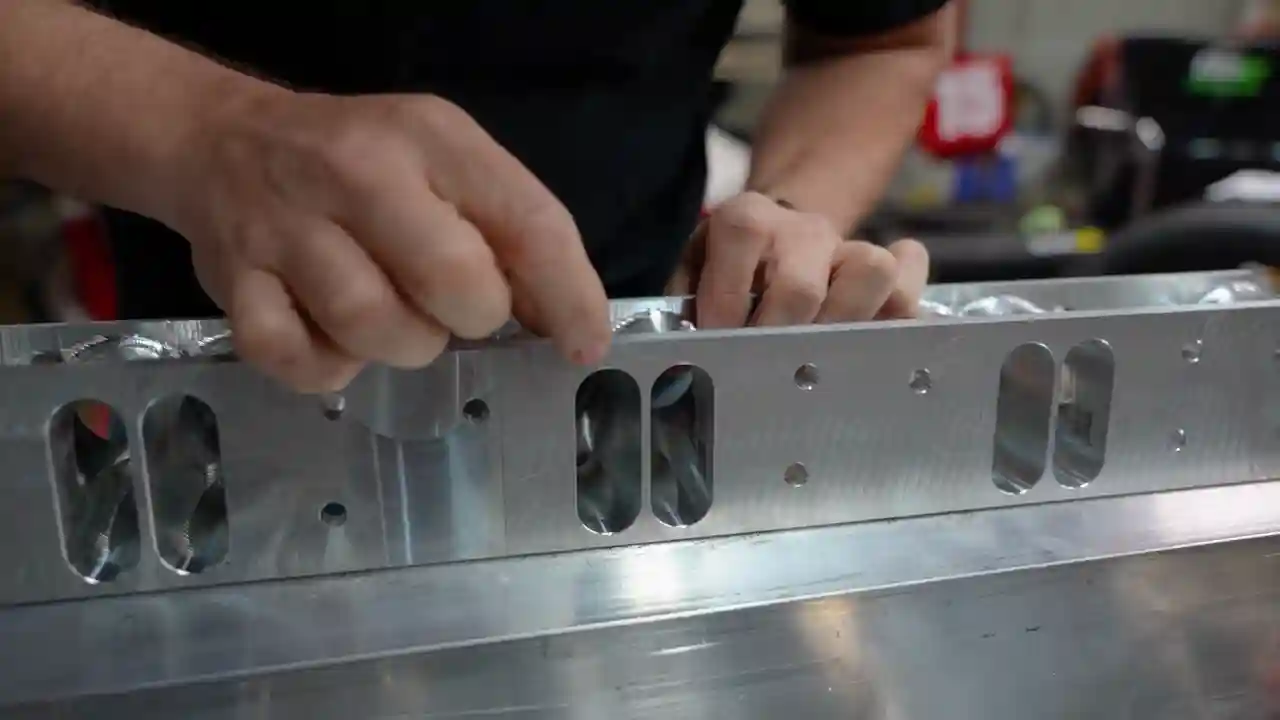
Image copyright Youtube
Watch Using AI to build the 12 ROTOR for 5000HP on Youtube
Viewer Reactions for Using AI to build the 12 ROTOR for 5000HP
Impressed with the fact that parts are being made in-house
Comparison to the engineering prowess of the Haas F1 team
Motor referred to as the "rotary final boss"
Advice to use machining wax for initial attempts and change coolant
AI praised for its use in engineering and science
Excitement for the 12 rotor update
Hack to improve visibility through door glass using tempered screen protectors
Appreciation for the high cost and endless fun of the build
Suggestion to explore topology optimization through FEA programs
Love for watching CNCs in action
Speculation on where the engine will end up
Praise for the channel's educational content and progression
Request for more rotary content
Discussion on topology optimization and AI
Advice to lower the part in the vices for stability
Inspiration from the level of engineering happening
Concern about the cutting fluid and suggestion to replace it
Complaint about the length of ads in the videos
Amazement at the progress made and comparison to Ford and Toyota
Appreciation for the camera work
Comment on the Keeps ad transition
Humorous comment about being "hard" for the build
Curiosity about what the AI would have come up with without specific instructions
Excitement for the project
Humorous comment about getting divorced due to the project
Questioning the benefit of AI in the design process
Speculation on what the engine will power
Comment on the complexity of the milling process
Suggestion to add pockets to make the part lighter
Suggestion to make the part in smaller, replaceable pieces
Humorous comment about the phrase "and it's hard... I'm hard"
Related Articles
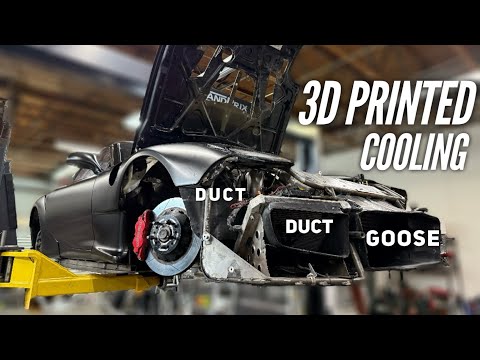
Rob Dahm: Shiny 3D Scanner, Clutch Kit, and 3D Printed Car Ducts
Rob Dahm showcases the Shiny 3D scanner's advanced capabilities, discusses a new clutch kit, and introduces Eight Sleep's innovative technology. The team delves into 3D printing ducts for the car, highlighting challenges and successes in the process.
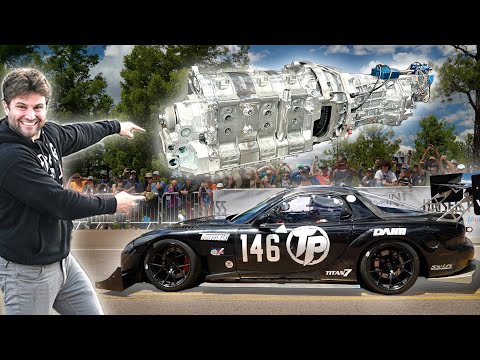
Rob Dahm's Team Revs Up Three-Rotor Engine for Pikes Peak Success
Rob Dahm's team prepares the three-rotor engine for Pikes Peak, overcoming challenges like rotor damage and seal issues. With meticulous rebuilding and innovative techniques, they enhance performance for the upcoming race.
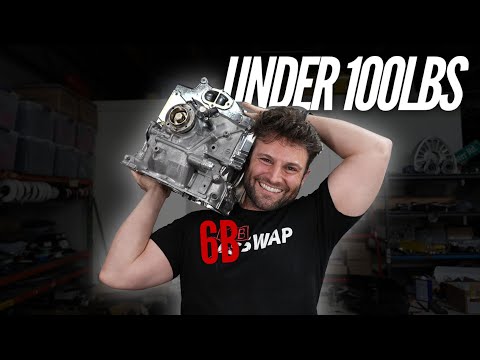
Building the Lightest Mazda Rotary Engine: Precision and Billet Components
Rob Dahm's team works on creating the lightest Mazda-based rotary engine ever, focusing on billet components and precision assembly for optimal performance.
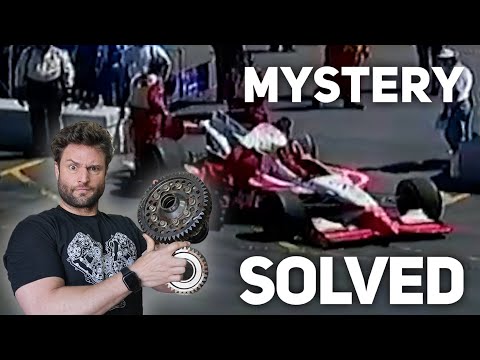
Reviving an Iconic Indie Car: Unveiling the Transmission Casing
Rob Dahm revives an iconic Indie Car, unveiling its versatile transmission casing. Discover the car's history, intricate mechanics, and the team's journey to restore it to its former racing glory.